In recent years, my country's molds have developed rapidly, and the technology has also been greatly improved, but there are still some gaps with the international level. When we use molds, there will be some failures, such as: molds will occur during the use of molds Burst, this is also a serious defect in mold technology in our country. What are the reasons for mold burst? The main points are as follows.
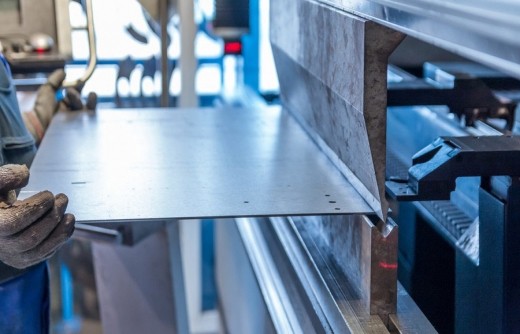
Stamping die
Analysis of the cause of mold burst:
1. The mold material is not good and it is easy to chip in the subsequent processing
2. Heat treatment: deformation caused by improper quenching and tempering process
3. The mold grinding flatness is not enough, resulting in flexural deformation
4. Design process: insufficient mold strength, too close knife edge spacing, unreasonable mold structure, insufficient number of template blocks, no pads
5. Improper processing of thread cutting: pulling thread cutting, wrong gap, no clear corner
6. Selection of punch equipment: punch tonnage, insufficient punching force, too deep adjustment of the die
7. Unsuccessful stripping: no demagnetization treatment before production, no return pin; there are jammed materials such as broken needles and broken springs during production
8. The blanking is not smooth: there is no leakage of feces when assembling the mold, or rolling to block the feces, and the feet to block the feces
9. Production awareness: lamination stamping, positioning is not in place, no air blow gun is used, and the template is cracked and production continues
How to prevent mold burst:
1. Stamping equipment
The accuracy and rigidity of stamping equipment (such as presses) have an extremely important impact on the life of the die. The stamping equipment has high precision and good rigidity, and the die life is greatly improved. Especially for small or no-clearance punches, hard alloy punches and precision punches, presses with high precision and good rigidity must be selected. Otherwise, the life of the mold will be reduced, and the chess tools will be damaged in severe cases.
2. Mold design
(1) The precision of the guide mechanism of the mold. In order to improve the life of the mold, it is necessary to correctly select the guiding form and determine the accuracy of the guiding mechanism according to the nature of the process and the accuracy of the parts.
(2) The geometric parameters of the cutting edge of the mold (convex and concave mold). The shape, matching clearance and fillet radius of the convex and concave molds not only have a great influence on the forming of the stamping part, but also have a great influence on the wear and life of the mold. For higher precision requirements, a smaller gap value should be selected; otherwise, the gap can be appropriately increased to increase the life of the mold.
3. Stamping process
(1) The raw materials of stamping parts.
①Use materials with good stamping processability as much as possible to reduce stamping deformation force; ②Strictly check the grade, thickness and surface quality of the raw materials before stamping, and wipe the raw materials clean, and remove surface oxides and rust when necessary; ③According to the stamping process and the types of raw materials, softening treatment and surface treatment can be arranged when necessary, and suitable lubricants and lubricating processes can be selected.
(2) Layout and edging.
Unreasonable reciprocating feeding layout method and too small overlap value will often cause rapid wear of the mold or damage to the convex and concave molds. The layout method and edge value must be reasonably selected according to the processing batch, quality requirements and mold matching gap of the parts to improve the life of the mold.
4. Mold material
①The use performance of the material should have high hardness (58~64HRC) and high strength, and have high wear resistance and sufficient toughness, small heat treatment deformation, and a certain degree of thermal hardness; ②Good process performance.
5. Thermal processing technology
The thermal processing quality of the mold has a great influence on the performance and service life of the mold.
(1) Forging process. This is an important link in the manufacturing process of mold working parts. The forging temperature range should be strictly controlled, the correct heating specification should be formulated, the correct forging force method should be adopted, and the slow cooling or timely annealing after forging should be used.
(2) Preliminary heat treatment. Depending on the materials and requirements of the mold working parts, preliminary heat treatment processes such as annealing, normalizing or quenching and tempering should be used to improve the structure, eliminate the structural defects of the forging blank, and improve the processing technology.
(3) Quenching and tempering. This is the key link in mold heat treatment. Special attention should be paid to prevent oxidation and decarburization during the quenching and heating of the die, and the heat treatment process specification should be strictly controlled. When conditions permit, vacuum heat treatment can be used. After quenching, it should be tempered in time, and different tempering processes should be adopted according to technical requirements.
(4) Stress relief annealing. For molds with high precision requirements, they need to undergo stress relief and tempering treatment after grinding or electrical machining, which is conducive to stabilizing mold accuracy and improving service life.
6. Processing surface quality
①During the processing of mold working parts, it is necessary to prevent the phenomenon of grinding and burning the surface of the parts, and the grinding process conditions and process methods (such as grinding wheel hardness, particle size, coolant, feed and other parameters) should be strictly controlled; ②The mold should be prevented during processing There are knife marks on the surface of the working part. Macro defects such as interlayers, cracks, and impact scars. The existence of these defects will cause stress concentration and become the root cause of fracture, causing early failure of the mold; ③The use of fine processing and fine processing such as grinding, grinding and polishing can obtain a smaller surface roughness value and improve the service life of the mold.
7. Surface strengthening treatment
In order to improve the performance and service life of the mold, the surface strengthening treatment of mold working parts is more and more widely used. Commonly used surface and strengthening treatment methods are: liquid carbonitriding, ion nitriding, boronizing, vanadium infiltration and electric spark strengthening, as well as chemical vapor deposition (CVD), physical vapor deposition (PVD) and in a salt bath Dip the surface of the workpiece with carbide method (TD), etc.
8. Wire cutting control of metamorphic layer
The cutting edge of the die is mostly processed by wire cutting. Due to the thermal effect and electrolysis of the wire cutting process, a certain thickness of metamorphic layer is produced on the surface of the mold, which causes the surface hardness to decrease, and microcracks appear. As a result, the wire cutting die is prone to early wear, which directly affects the die blanking gap. Keeping and cutting edges are easy to chip and shorten the service life of the mold. Therefore, reasonable electrical standards should be selected in the online cutting process to minimize the depth of the metamorphic layer.
9. Correct use and reasonable maintenance
In order to protect normal production, improve the quality of stamping parts, reduce costs, and extend the life of the die, the die must be used and maintained reasonably, and the die "three inspection" system must be strictly implemented (inspection before use, inspection during use and inspection after use), and do Good die and maintenance work.